A second focus is the process for recycling lithium-ion batteries, which has been tested in various reference cases. BHS will present exhibits related to this process, such as a rotor impact mill with a new hammer design, a horizontal dryer, and a separating table.
The goal is clear: to recover valuable resources. To this end, the Sonthofen-based group of companies continuously invests in future-oriented technologies and novel process solutions that enable customers to extract maximum value, especially when recycling metalliferous composites and industrial waste. At BHS’ trade show appearance at IFAT 2022, the focus will be on the fine processing of various metal-containing residues, such as Automotive Shredder Residue (ASR), e-scrap, and incinerator bottom ash (IBA). “BHS-Sonthofen has further developed its fine preparation process with extensive tests, thus further improving output quality,” explains Daniel Weber, head of the Recycling & Environment division. “The process works just as well for ASR, taking into account material-specific requirements, as it does for the fine processing of all other metal-containing materials such as electrical and electronic scrap or cable remnants.”
New hammer design of the rotor impact mill – higher output quality
The heart of the fine preparation process is the rotor impact mill, which BHS is presenting with a new hammer design at the trade show. The RPMX type rotor impact mill is a high-performance crusher unique in its field, setting standards in fine processing and metal recovery with its impeller rotor and special anvil ring. The machine reliably separates material composites and removes cable sheathing and other substances that adhere to metals. The new hammer design of the rotor impact mill significantly optimizes disaggregation and shaping of the output – while simultaneously reducing wear. Due to the improved output quality, fewer or shorter passes are required, which results in higher throughput. In addition, BHS is presenting a new maintenance concept for the machine that simplifies maintenance and inspection work by the operator and, in combination with the new hammer design, ensures high machine availability.
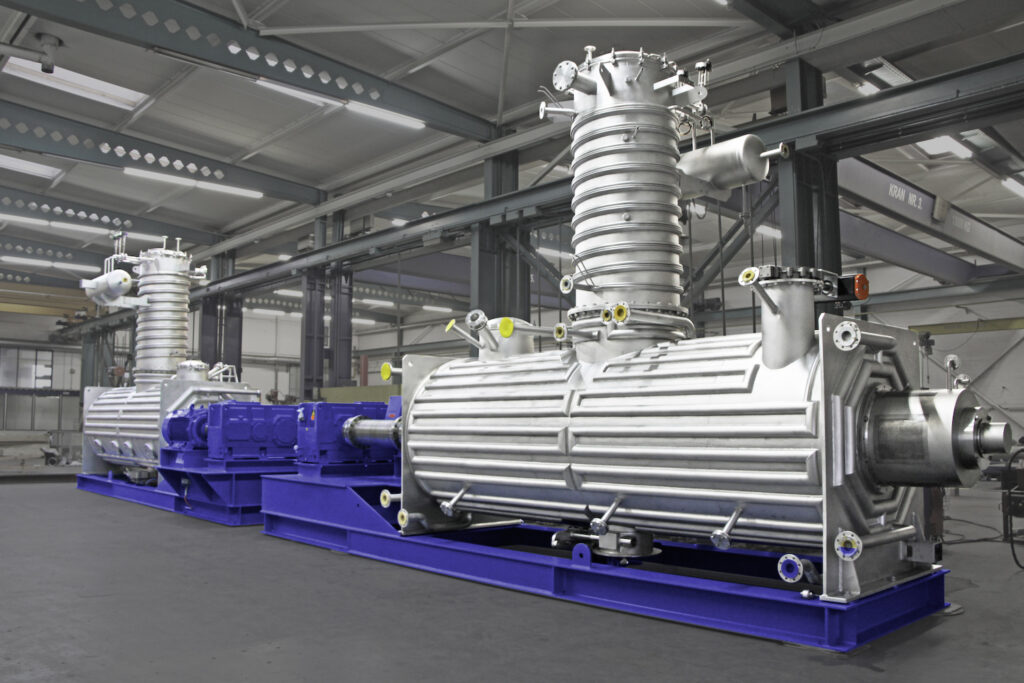
Proven, innovative recycling process for lithium-ion batteries The company’s second focus is on the recycling of lithium-ion batteries. For this purpose, BHS has developed a complete mechanical solution that focuses on a high recovery rate of the resources it contains. The process has already been tested worldwide in existing reference plants run by prestigious customers. Thanks to the consistently inert process, from the crusher to the dryer, hazards such as fires or the escape of toxic gases can be avoided. Trade show visitors can expect to see the HTC 140 type horizontal dryer used in this process at IFAT. In the process, the dryer applies a vacuum and heats the pre-crushed batteries to safely evaporate potentially toxic components. The crushed batteries are no longer hazardous after the drying phase.
Separation technology and pre-shredder round off trade show presentation
From the new technological field of separating, sorting and classifying technology, a separating table from BHS and RW Recycling World will be on display at the booth. BHS-Sonthofen has held a stake in the Swiss company since 2021. This cooperative venture allows products from separation, sorting, and classification technology to be integrated into processes from BHS in order to offer solutions from a single source – for example, in the fine preparation process. With the depth of added value and process competence thus expanded, the Sonthofen-based group of companies has further strengthened its position as a technology leader for the recycling of metalliferous composites and industrial waste.
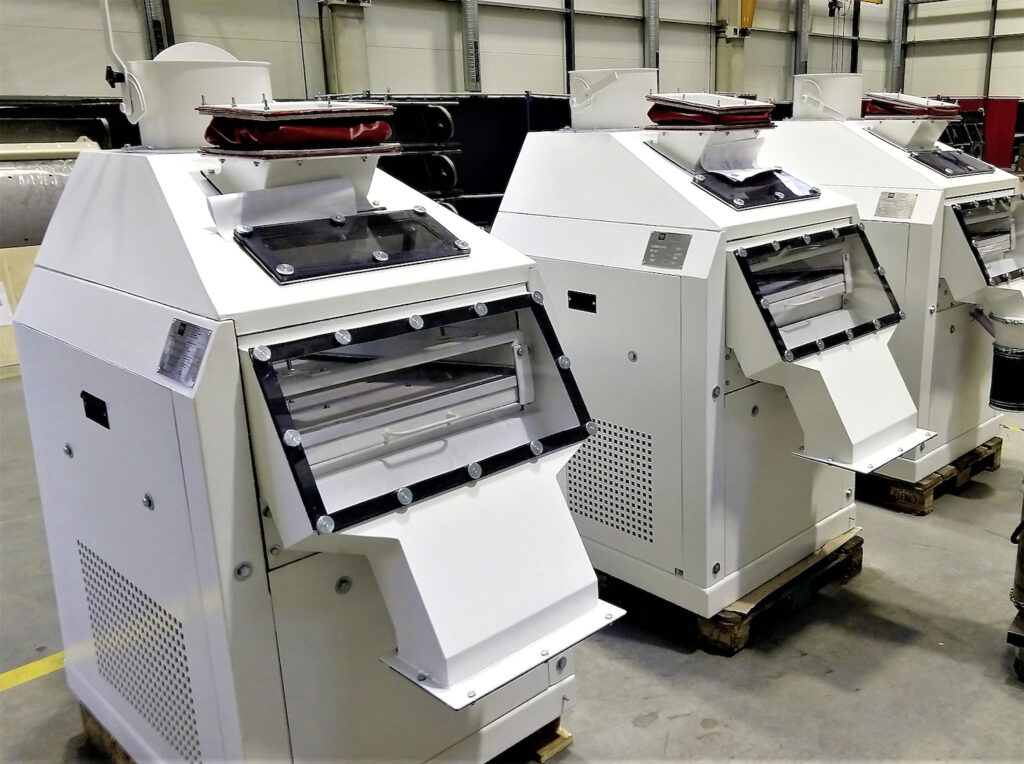
BHS rounds off its trade show presence with the virtually exhibited RAPAX pre-shredder. The powerful machine, which was launched last year, can be used universally: In its various designs, it is suitable for processing metal fractions, commercial and industrial waste, and construction waste. With this machine, BHS combines design and function and takes pre-crushing to a new level.
BHS-Sonthofen at IFAT: Booth B4-351/450 in Munich from May 30 to June 3, 2022