Improving bale weights for transportation was one of the key drivers. With their equipment housed in a relatively small building, they had to get creative!
The council had to identify solutions which would help them improve the bale densities of plastic and cardboard waste. They were operating a small Twin Ram baler which produced an American-style wide mouth bale. Once bales were loaded on to a lorry for transportation, the low bale compaction meant that space wasn’t optimised. As the footprint of the building was quite small, the council were unsure of what could be achieved.
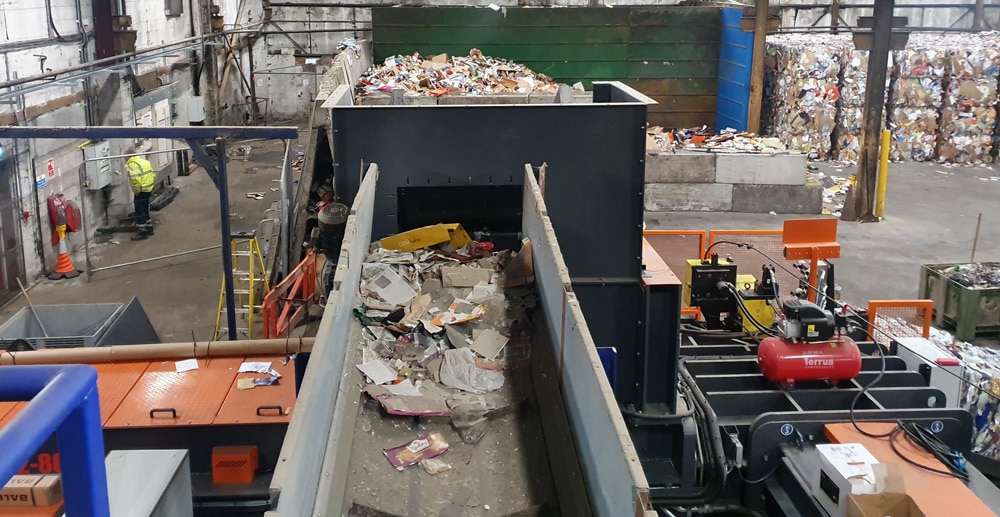
Designed to Fit
The council consulted with Northern Ireland based, CK International – a leading manufacturer in balers and compactors. Following a site survey, CK International soon realised “a one-size fits all” approach would not work here. The MRF, located in Keynsham, Bristol, has a small footprint, so 3D drawings with various options helped to visualise the end result.
CK International knew that a CKTR82-80T-74kW Twin Ram fully automatic baler would certainly increase the weight of the council’s cardboard and plastic bales. However, it was clear to all involved, that this machine would need customised to suit the space.
The manufacturer set about creating several solutions. They firstly designed and manufactured an automated bale push ram which moved the bale through 90 degrees, providing optimal process flow. Installing the power pack to the side of the machine ensured best use of the limited space available. They also adapted other elements to best suit the existing conveyors.
CK International also installed a new chain drive conveyor and re-engineered the picking cabin. This provided more space to allow for an extra picker on the quality belt. They also supplied access ladders and hand railings.

Remote management
With installation work carried out over a weekend and fast set-up, the council could see significant benefits immediately.
They opted to use the cloud-based CK Baler Management System which provides up-to-date, accurate information on the efficiency of their machine. This data, such as bales produced per hour and quantity of wire used per bale, allows the council to determine the productivity and capacity of the baler.
Simon Porter, Head of Fleet & Waste Operations at Bath and North East Somerset Council says:
“CK International knew exactly what we needed and how they could help us get the best out of this facility. They adapted equipment to suit us and our building which was crucial. The reliability of the unit is superb and the back-up service and response we receive from CK International gives us that extra confidence.
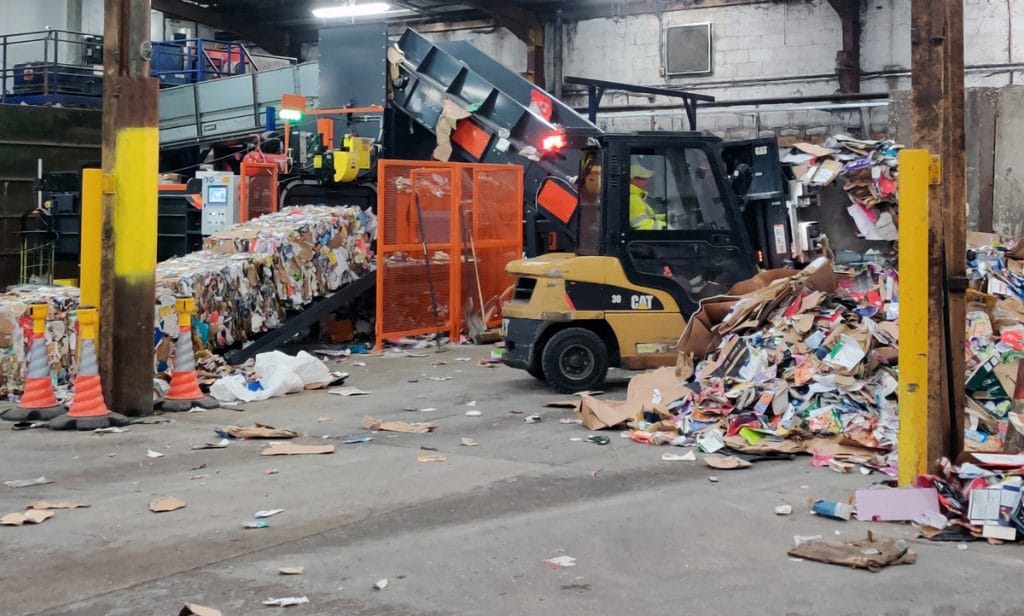
We have certainly increased productivity at the site and improved bale weights. The plastic and cardboard are now achieving weights of up to 500kg and 550kg per bale, respectively. In terms of capacity, the machine is consistently baling cardboard and paper at rate of up to 8 tonnes per hour and plastics at circa 5 tonnes per hour. The difference in weights and density of the waste material means bales are loaded more efficiently on to lorries, thus reducing forklift movements on site.
One of the added benefits for us is the remote management portal. This allows us to login remotely and monitor the productivity of the baler. In the current climate, this has been invaluable.”