Pioneer Wiegand-Glashüttenwerke GmbH
In October 2022, Wiegand-Glas, one of the largest family-owned glass manufacturers in Germany, took possession of REDWAVE’s Qi, the first quality control system engineered to fit into a mobile shipping container. As clean cullet is the most important raw material in glass production, and high-quality cullet is a prerequisite for a strong final product, contaminants such as ceramics, stones or porcelain can instigate massive financial loss in glass production. Additional impurities found in heat-resistant and non-melted glass-ceramic particles can slip into the cullet, leading to weaknesses in the newly produced glass and increasing the probability of shattering. In order avoid these impurities, Wiegand-Glas invested in REDWAVE’s mobile container-housed quality control system: the REDWAVE Qi.
This system is designed to be independent but is set-up as either mobile or stationary units and can be integrated into an existing sorting system. Soon to be processed material is examined, controlled and evaluated via a REDWAVE Qi analyzer to determine the quality of the cullet before actual glass production commences. By testing the material composition, the REDWAVE Qi can provide much needed information regarding the quality of the input material. This step allows for the discovery of unwanted impurities which can later create weaknesses in the final glass product.
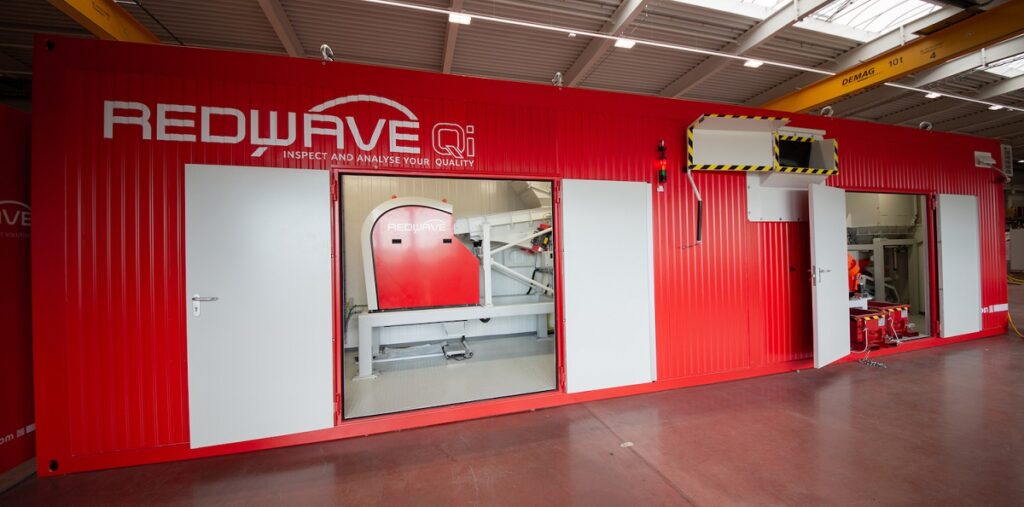
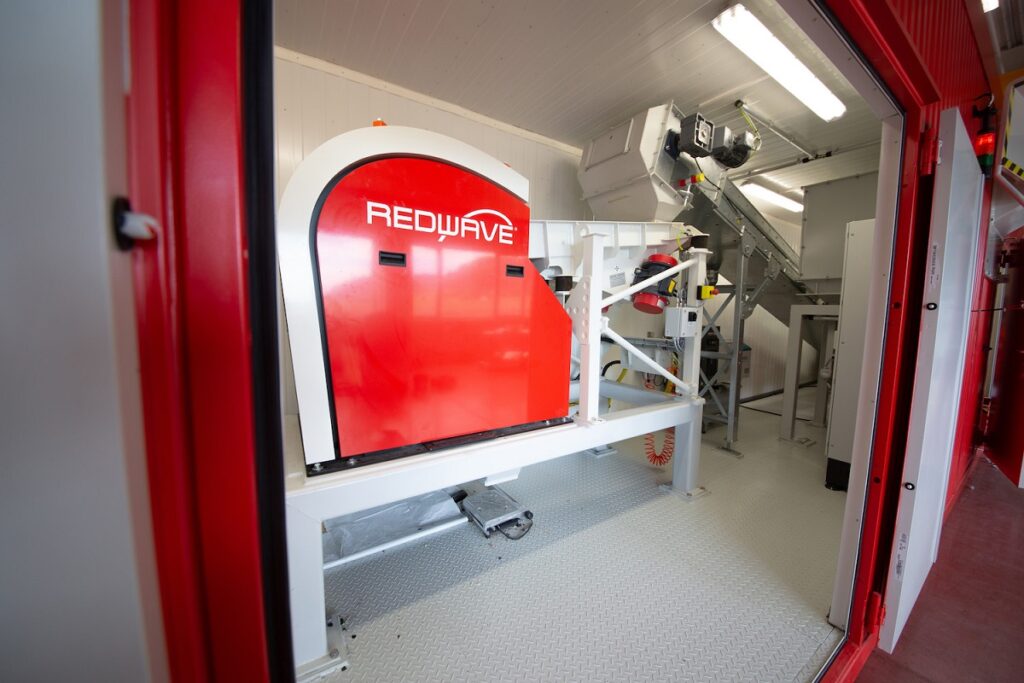
How it works – functioning principle
If REDWAVE Qi is permanently integrated in a sorting system, quality assurance and quality control are already carried out during the sorting process. In the mobile shipping container variant, a pre-determined, unscreened sample is transported via a conveyor belt into the machine for analyzation. The sample is examined, and the impurities are ejected for further analysis. The material, as well as the ejected impurities, are weighed in order to determine the contaminant content and then re-evaluated.
This detailed evaluation takes place via the system itself or digitally via the REDWAVE mate software; both serve as verification of product quality. Alerts are issued if thresholds are exceeded or fall below the specified requirements. The system provides information about the nature of the material, the grain size, the weight, the color distribution or the material composition. If the tested and analyzed material meets the requirements of the glassworks, it is used in new glass production. If the material does not meet the requirements, the material can be rejected by the glass producer and returned to the cullet processor for additional sorting. This saves the glass producer both time and money.
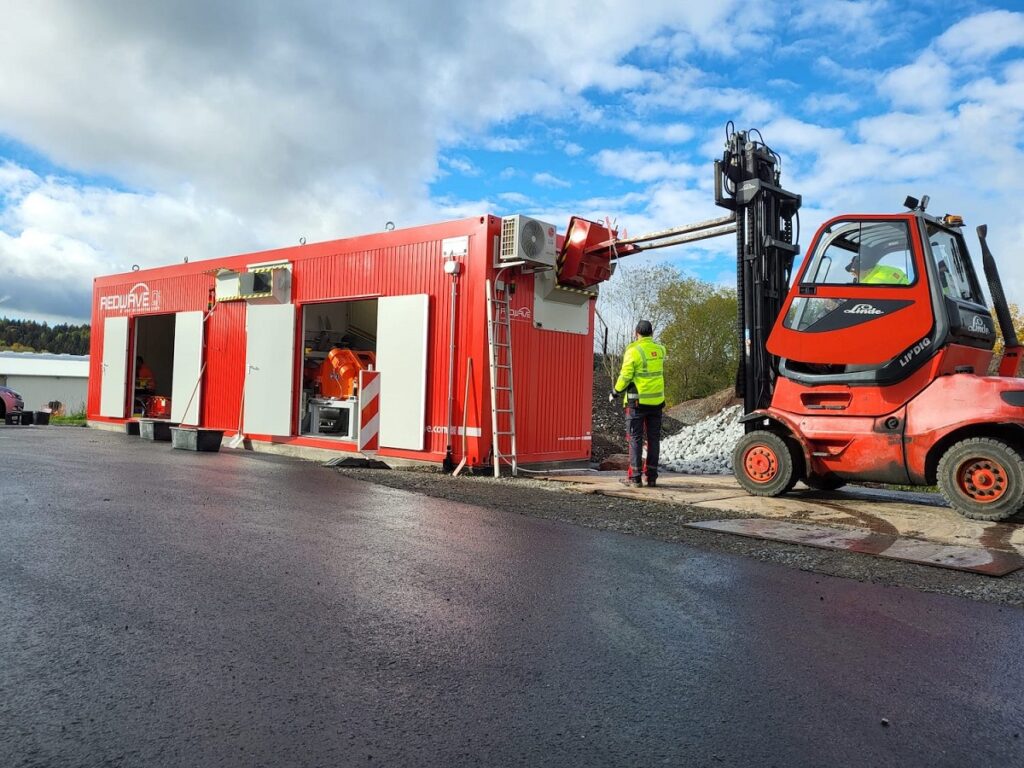
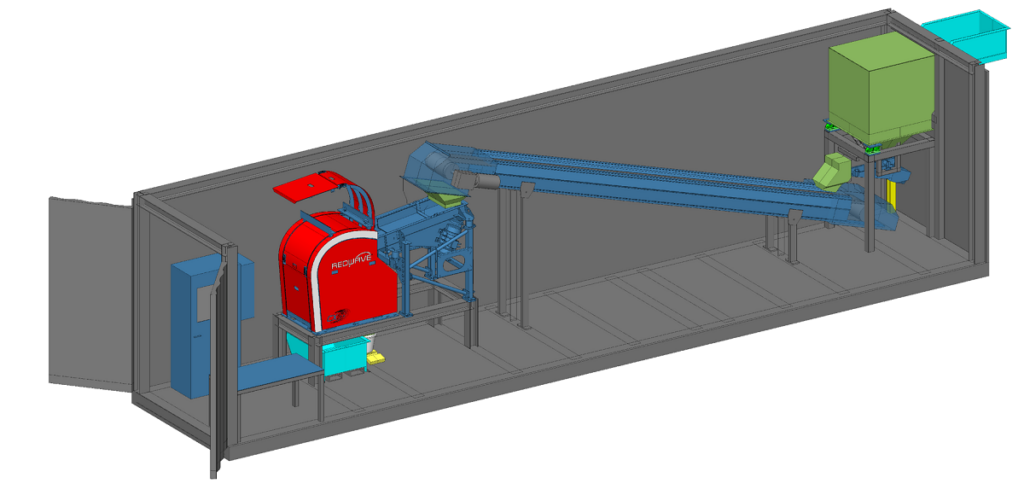
Different analysing systems:
REDWAVE Qi can be designed as a mobile container solution, stationary integrated into a plant or, as a single analysis system.
As a stand-alone, mobile container solution or integrated into an existing sorting plant, the system is increasingly used in glass recycling or in glass production for quality control. The analysis evaluations serve as proof of the quality of the cullet.
Executed as single analysis system, the processed material is analysed, controlled and evaluated by REDWAVE Qi. Based on the material surface, the material composition is determined in order to output calorific values, heating values and material moisture for refuse derived fuel processing plants. This data output is indicated online via the REDWAVE mate software. The material data composition includes chlorine values, RDF details and purity confirmation for the original input material. This allows a comparative measurement with, for example, values from incineration or chlorine analysis in the laboratory.
- 1. Mobile container solution – flexible, mobile and cost-efficient
The container is pre-assembled mechanically, electrically and pneumatically, at REDWAVE’s warehouse, which eliminates cost-intensive on-site assembly times for the customer. If the conditions at the existing location change or if the container is needed in another system, it can be easily moved and quickly installed elsewhere.
- 2. Stationary integration into the glass processing plant
An input material sample is continuously taken from the product stream, during the ongoing sorting process, to ensure the quality of the final product. The sample quantity is controlled by the setting of the opening time, and opening frequency of the flap, and can be up to 10% of the total input. An additional advantage of quality control is that the continuous analysis and control of the material makes troubleshooting in a sorting system much easier (e.g. for the screen mats or the sorting machines). Stationary integration ensures the full functionality of the system and targeted data evaluation makes it possible to increase plant efficiency.
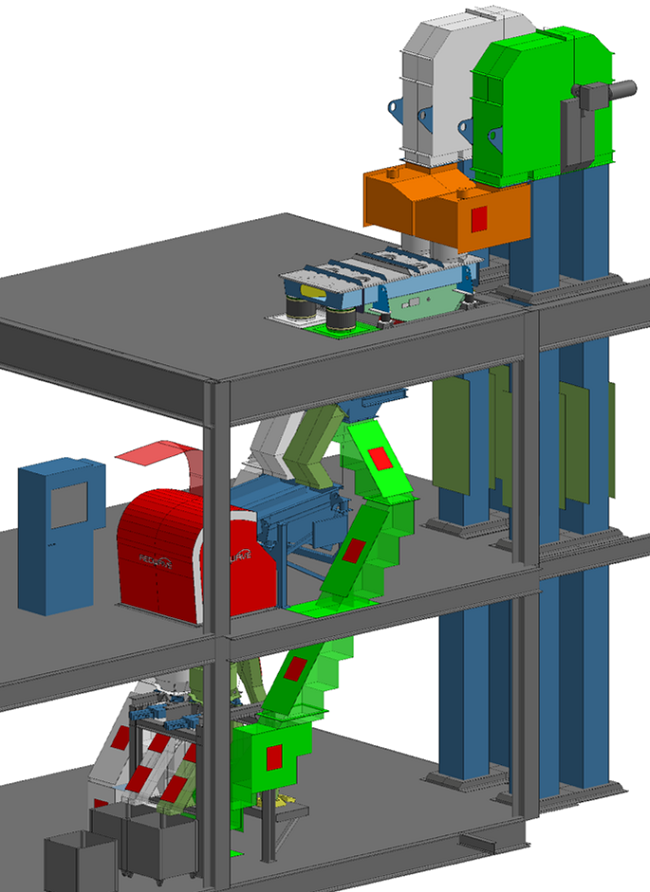