Differentiating materials with the highest quality is the basis for future production and processing steps. MSTVision delivers a high-speed sorting technology that guarantees a precise separation of the material.
Highest precision
To ensure a precise separation, a minimum delay time between image acquisition and rejection is advantageous. This high-speed sorting technology achieves delay times of 1ms due to FPGA accelerated signal processing. So the actuators can be placed directly behind the scan line to minimize changes of the motion vectors of the material until rejection.
All functions of the MSTVision technology platform are implemented in the FPGA of a Silicon Software framegrabber. This includes image acquisition of a line scan camera, image processing as well as the exact delay of the reject signals. Even the precise control of the actuators is done directly from the framegrabber using electronic boards provided by MSTVision. This allows full CameraLink bandwidth to be processed, i.e. a line rate of 100kHz can be achieved for an 8k camera (resolution of 8,192 pixels). This corresponds to a processing speed of 800 million pixels/s. Development of CoaXpress is ongoing and release is planned for Q1/Q2 2021.
Since all steps are executed in the FPGA, almost no computing power is required from the host PC except for the optional visualization.
Multispectral separation
The use of the longterm-proven MultiChannel technology allows the image acquisition of multispectral images in only one run by time multiplexing of fast triggerable line lights. Any wavelength the camera sensor is sensitive to (UV, VIS, NIR, or SWIR for InGaAs cameras) can be chosen. Separation based on the spectral properties of the material is thus possible. An example is shown in Figure 1, where the material is separated by the information of four image channels illuminated with different wavelengths.
Since the line lights are usually based on LEDs, they emit a wavelength band instead of a single wavelength. An overview of typically available LED lightings is shown in Figure 2.
Additionally, any other typical illumination arrangement (i.e. darkfield/brightfield) can be combined to get even more information for classification.
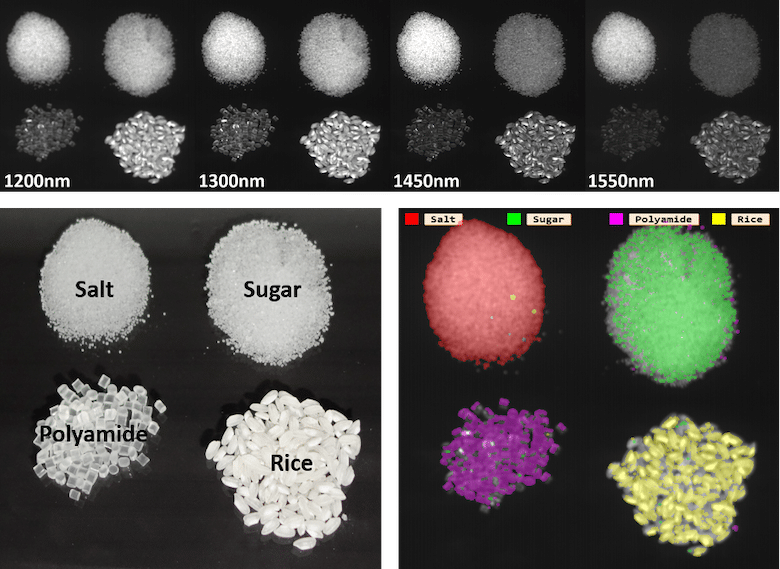
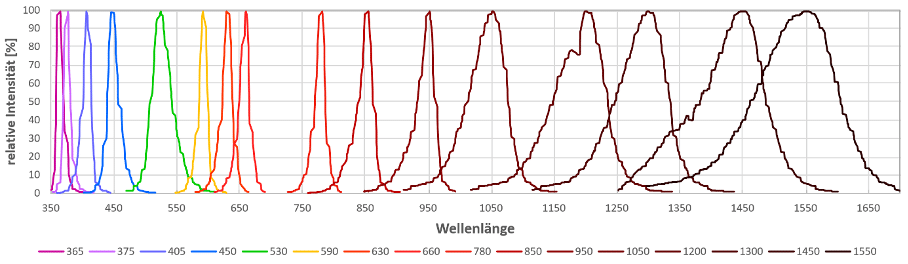
Modular system design
A range of optimized hardware components, shown in Figure 3, provides a highly performant connection between framegrabber hardware and different actuators like high-speed pneumatic valves (MATRIX mechatronics, Festo, SMC …). The modular system uses standard cables for easy integration and allows system designs from 32 to 1024 outputs per framegrabber at a variable frequency (typically 1kHz).
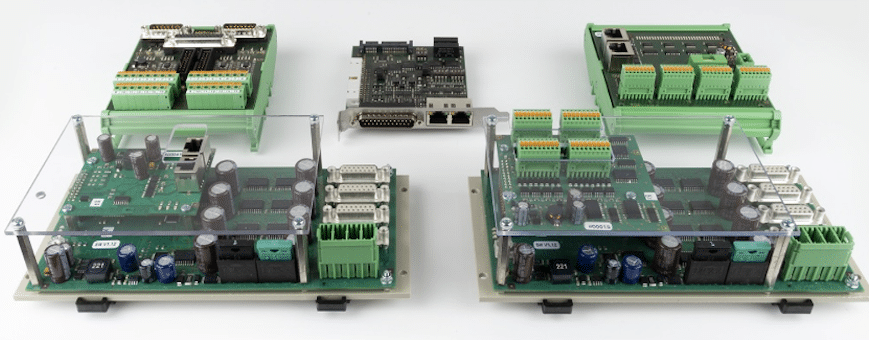
Any number of cameras can be operated in parallel on a corresponding number of framegrabbers. This also scales the maximum number of actuators (max. 1024 per framegrabber). Overlapping areas of adjacent cameras, where actuators are controlled by different framegrabbers, are possible without any electrical problems.
Customer-specific algorithms and other features may be implemented within the FPGA either as a development service provided by MSTVision or by a customer.