What was initially perceived as a highly underestimated niche product by the competition has become a reliable problem solver for users. A realization that competitors have now also recognized and are now seeking a piece of the pie. It is no longer a secret that the first comparison models are circulating on the market, and it is also no secret that further duplicates from well-known manufacturers are going to follow.
“Our goal is to keep the IMPAKTOR model series competitive and future-proof despite increasing pressure from the competition,” promises Norbert Hammel, founder and innovative visionary at ARJES. “Therefore, the IMPAKTOR 250 product has already evolved into its successor model IMPAKTOR 250 evo in 2018 and now, four years later, it will receive another significant evolutionary leap.
From now on, ARJES will exclusively offer the successor version IMPAKTOR 250 evo II at the established “best price-performance ratio” in its class. Through the innovative optimizations of the successor model, ARJES sees its chance to remain the market leader in this price class.
The most important optimizations of the IMPAKTOR 250 evo II
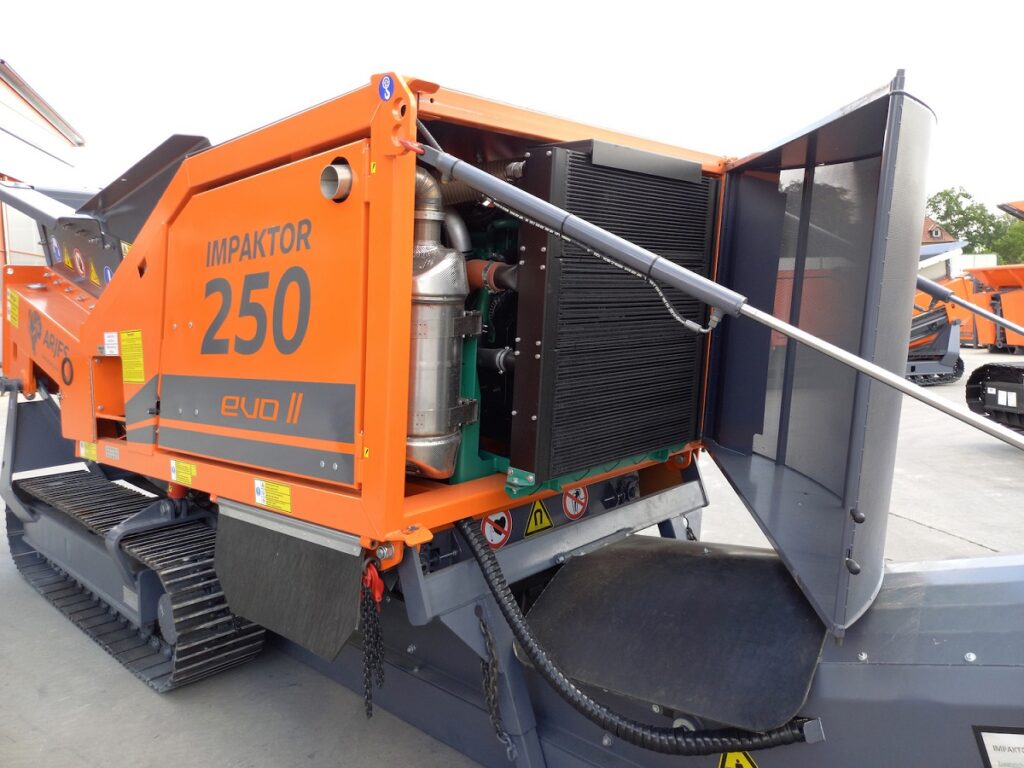
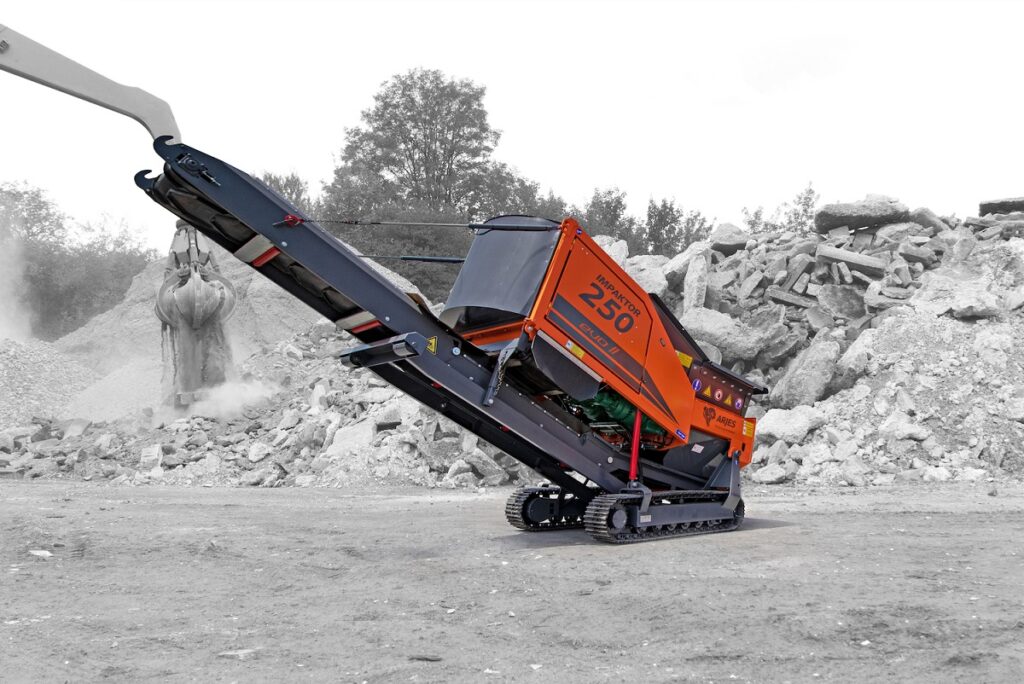
Improved transport capabilities
In the successor version, the transport height has been reduced to only approx. 255 cm and is thus approx. 20 cm lower than in the predecessor model. Sea container loading may be carried out without dismantling the hopper wall, and the maximum loading height for trucks is generally not exceeded. The firmly bolted and extended base frame rests on a large surface during loading and, therefore, ensures greater transport safety.
More powerful shredding shafts and revised quick-change cassette
Due to the improved quick-change cassette for the shafts, pressure is no longer exerted on the fastening bolts during the crushing process, as the full load is now transferred to the crushing table as well as the entire machine. In combination with the optimized concrete shafts, which work much more aggressively than before, the overall package for the IMPAKTOR 250 evo II twin-shaft crusher is even more powerful.
New innovative crushing bar system
The new waveform plates are characterized by the fact that they are arranged as individual parts under the shafts and act as counter blades. By inserting or removing them, the gap width may be modified and thus the final grain size adjusted. In the case of a worn cutting blade, the plate can be rotated several times until all four edges are completely worn out. The separately mounted hopper frames and walls can be placed on either the right or left side of the shredding unit.
Height adjustable overband magnet
Featuring a height-adjustable permanent magnet, the distance may be adjusted by using a chain suspension, thus defining the separation of ferrous material. An additional rubber cover protects against the ejection of ferrous parts and, as a result of the hinge bar, also provides a view into the motor compartment for cleaning work. Another bonus is the compact discharge bin for ferrous parts, which can be easily attached to the provided retaining points.
Simplified maintenance and servicing
The new semi-circular radiator grille above the discharge conveyor consists of a perforated grid, which provides more intake volume. Another advantage is the folding function of the grille, which ensures optimum accessibility to the engine for service, maintenance and cleaning. In general, the new IMPAKTOR 250 evo II successor version is designed in such a way that all wearing parts can be easily replaced, refurbished, or reused several times, resulting in significant cost savings in both manufacturing and maintenance.