Caring for the environment and sustainability is paramount. To reduce waste, hydraulic presses are essential and indispensable equipment for any recycler who wants to optimize profit margins. In this sense, all manufacturers try to innovate in their baling presses in two ways. On one hand, by increasing production and introducing improvements that can lower pressing costs, optimize press weights and times. And, on the other hand, reducing wear, maintenance costs, and possible breakdowns, thus increasing the availability of the balers in operation through improvements in the hydraulic, software, and construction elements.
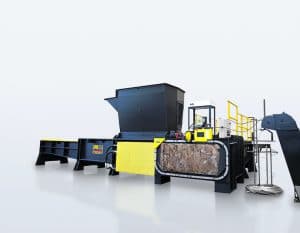
In the sorting plants, the Two Ram balers are gaining relevance, by allowing either the baling of recyclables (plastic, cardboard, paper) or non-ferrous materials (e.g. cans, profiles, radiators, etc.) in large packages to optimize their handling and storage.
These balers are also prevailing over the horizontal presses in the RDF (Refuse Derived Fuel) sector since they allow shrink-wrapping the bale without having to use wire, which entails great savings in wire, in addition to complying with the current law that requires the shrink-wrapping of this material.
Finally, there are innovations in the programming and software to monitor the operation of the presses and even export operating data to other devices such as computers, tablets, smartphones and other systems. In the end, equipment is more and more integrated into the network and exploiting the advantages of advances in digitization.