As part of Veolia Nederland B.V., Aufderhaar Kunststof Recycling B.V. has taken a firm place in the field of plastics recycling. Fifteen workers are employed in an area of approximately 11,000m2. The company mainly recycles polyethylene (PE) and polypropylene (PP). This includes plastic packaging materials and household waste as well as plastic flowerpots, most of which come from the Netherlands and Europe.
Performance and reliability in continuous operation
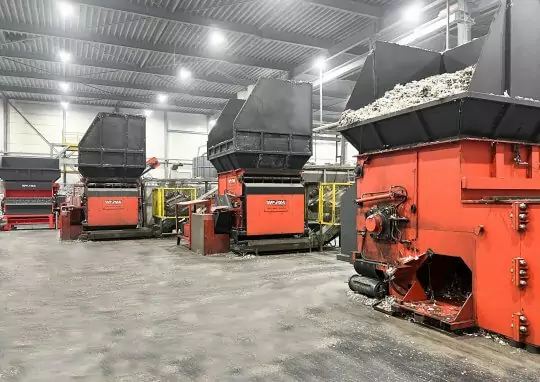
“When we recently decided on our fourth machine, the WEIMA W5.18 single-shaft shredder, we knew from our own experience that we wanted a reliable machine that would meet our high demands,” says Sebastiaan Kok, production manager. “The rock-solid construction, together with the high performance of the drive, convinced us that this was the best choice for our requirements. And if maintenance is ever needed, the direct rotor access via a wide opening gives us plenty of space to work. This saves us valuable time.
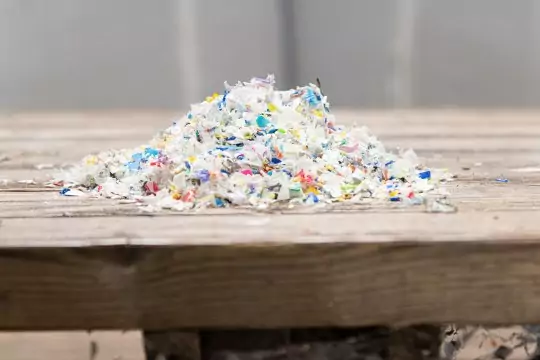
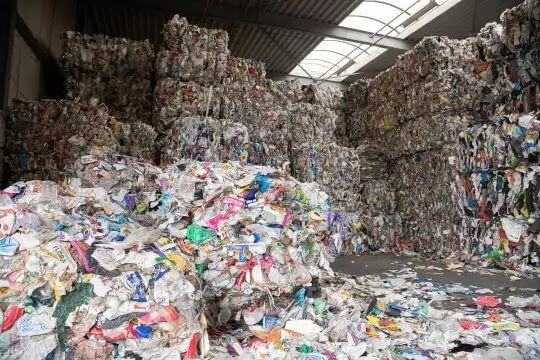
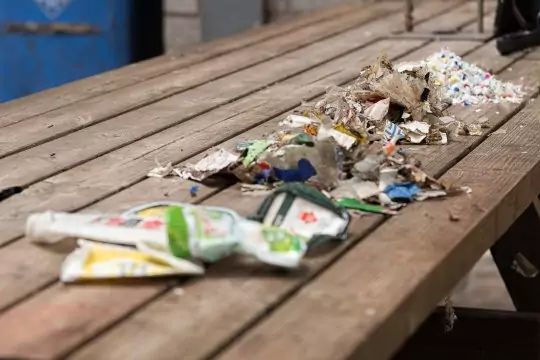
All shredders within the four recycling lines are used continuously in this three-shift operation. They are filled with the help of wheel loaders that transport pre-shredded material into the large hopper openings of the WEIMA shredders around the clock. Aufderhaar changes the rotor blades every 250 hours, depending on the material, to ensure a consistently high throughput.
Loyalty pays off fourfold
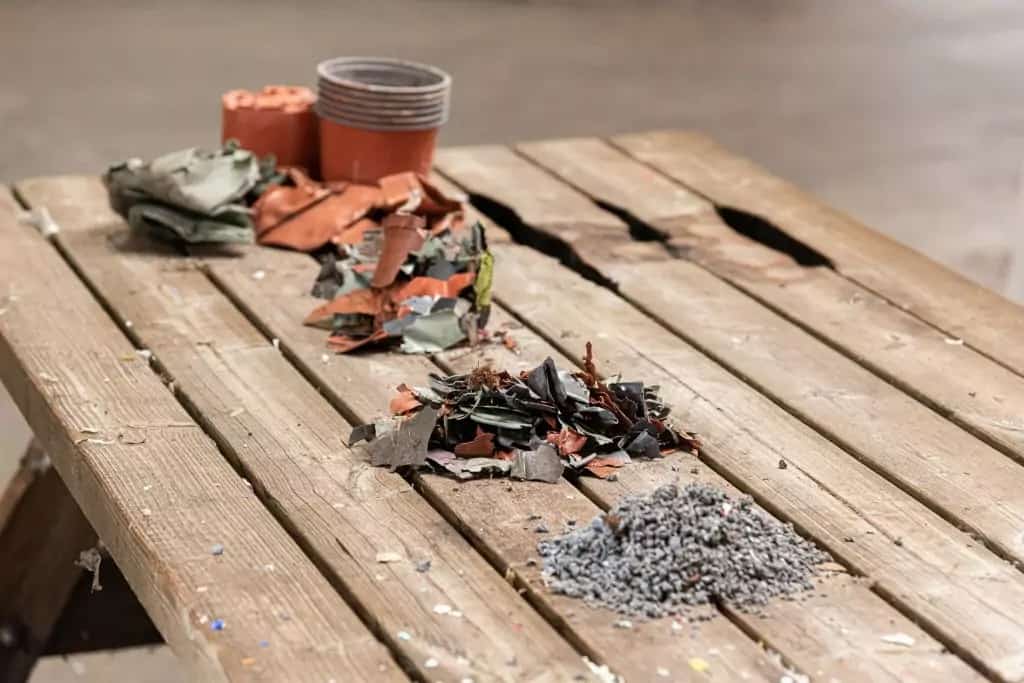
The Dutch recycling expert can now call four WEIMA shredders its own. The first two plastic shredders were integrated into the production lines in 2018. The third followed two years later and finally the fourth in 2022. Further investments are already being planned. The most recent machine is used by Aufderhaar mainly for the preparation of polypropylene flowerpots. An innovation, as Sebastiaan Kok reports:
“With the W5.18 shredder from WEIMA, we are now ideally positioned to carry out flowerpot recycling efficiently. After the pressed bales have been pre-shredded, the W5.18 shreds them to a homogeneous flake size. The built-in swing-arm pusher (we would say “swing ram” instead of “swing-arm pusher”) presses the material against the rotor in a load-dependent manner. The flakes are then washed and extruded. We are very proud that we can contribute to the circular economy with our plants and that new, recycled products are created with the help of our work.”
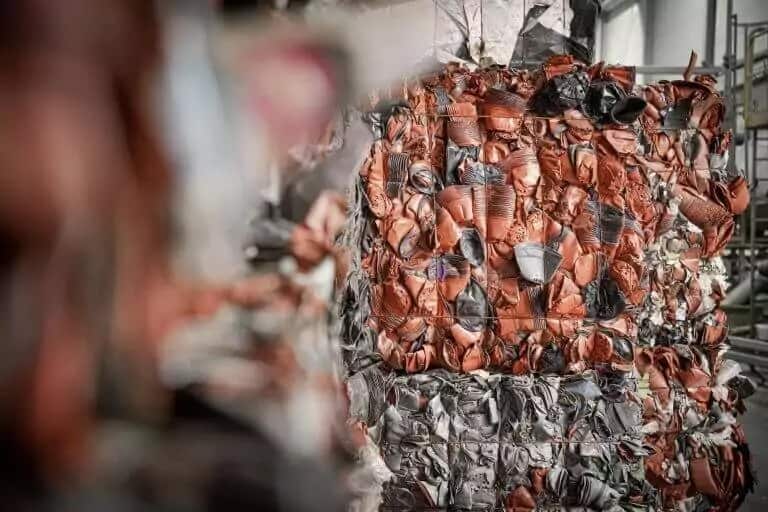
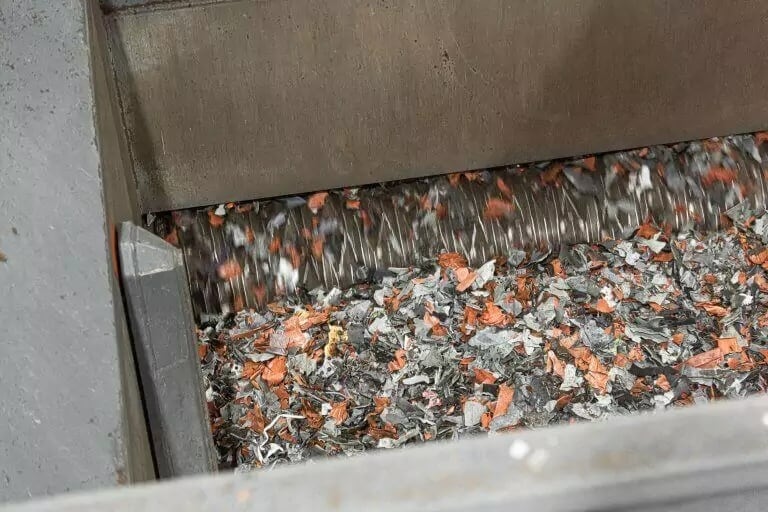
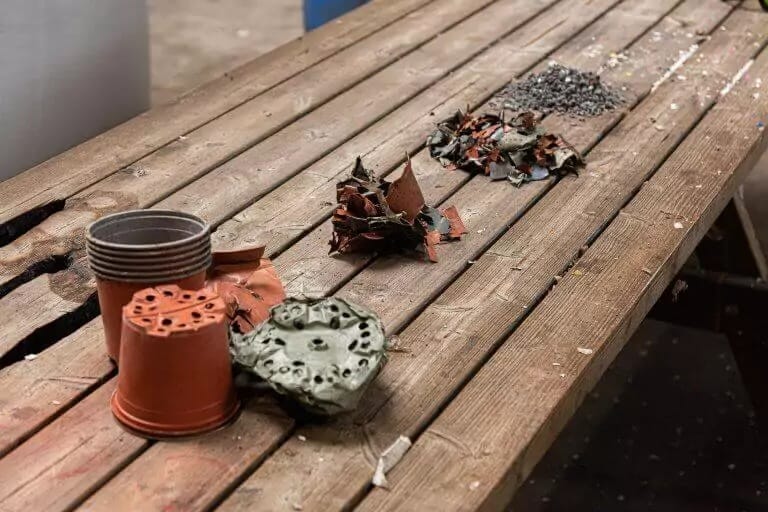