Plastics markets and requirements
In a time where seemingly every month a plastics recycler goes out of business, it may seem counterintuitive to invest in this industry. “But we don’t see it that way”, says Jelle Saint-Germain, sales engineer at Ad Rem. “None of our existing systems has been shut down, despite the economic downturn for plastic recyclers. It reaffirms that if you focus on the right products and create a high-quality end product, the value is there.”
At Galloo, Ad Rem’s parent company, plastics have been recycled since the ‘90s. Part of it is WEEE plastics, including fridges and SDA (Small Domestic Appliances), but the main business lies in ASR plastics – automotive shredder residue, a notoriously hard fraction to recycle. This is where the Galloo / Ad Rem process truly shines. “What Galloo does is taking a very polluted and mixed fraction, extracting and cleaning the PP from it, and turning it into pellets that they sell back to the automotive industry”, says Saint-Germain. Galloo is involved in a Joint Venture company SUSTAINera VALORAUTO SAS with Stellantis to manage the takeback from End-of-Life Vehicles in Europe. “The recycled PP from Galloo is not only found in Stellantis cars, but in several other large car brands. In Japan, a Toyota Tsusho subsidiary company called Planic is using the Ad Rem process to recycle their ASR plastics locally”. Aside from PP, the PE, PS and ABS are also recovered and recycled.
But WEEE and ASR are not the only applications for Ad Rem’s plastic separation technology. With the new test and development center, it will be possible to tap into other markets. “We get regular requests from the Construction and Demolition sector, but so far we’ve always arrived at a dead end, mainly because we don’t know how these different materials are going to behave in our process”. Other examples include PVC recycling: for WEEE or ASR, the target plastics float in the sink-float process, but in the case of PVC recycling, the valuable materials are in the sinking fraction and the pollution can theoretically be floated off. “This cannot be tested on our existing installations without severely disrupting the operations of our customers’ plants. For applications like this, our test and development center will come in very handy”.
New headquarters
Valtech, Ad Rem’s other parent company (Ad Rem is a 50/50 Joint Venture between Valtech and Galloo), has recently finished the construction of a new building. The building is a 6000 m² facility that houses the Valtech staff as well as Ad Rem and sister company Motus Handling in 1400 m² of office space. With the construction of the workshop also came Ad Rem’s need for a test and development center.
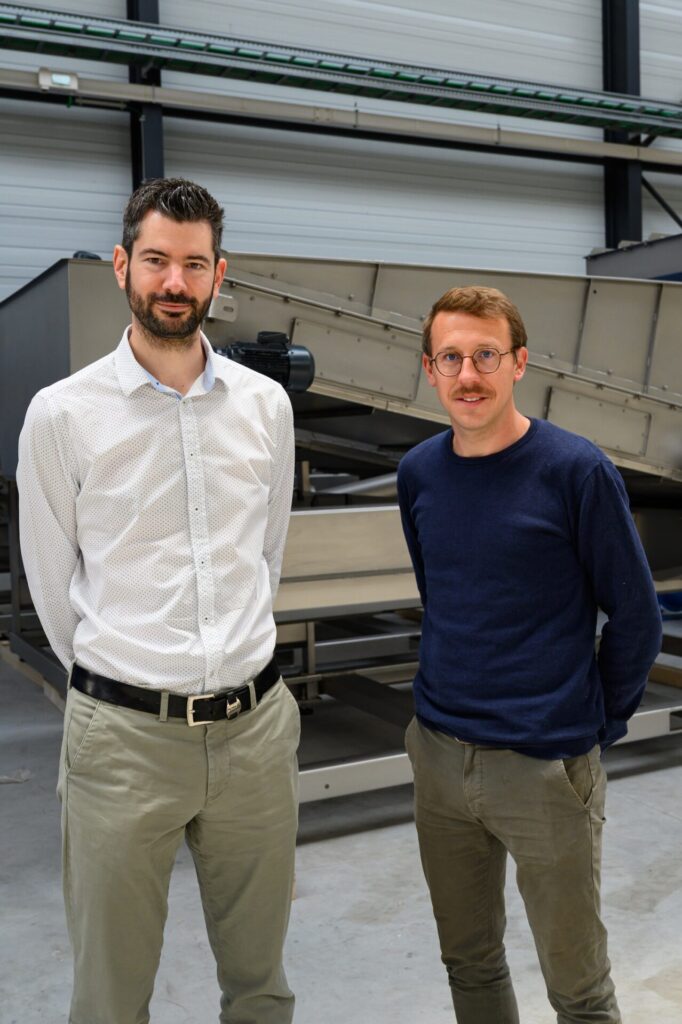
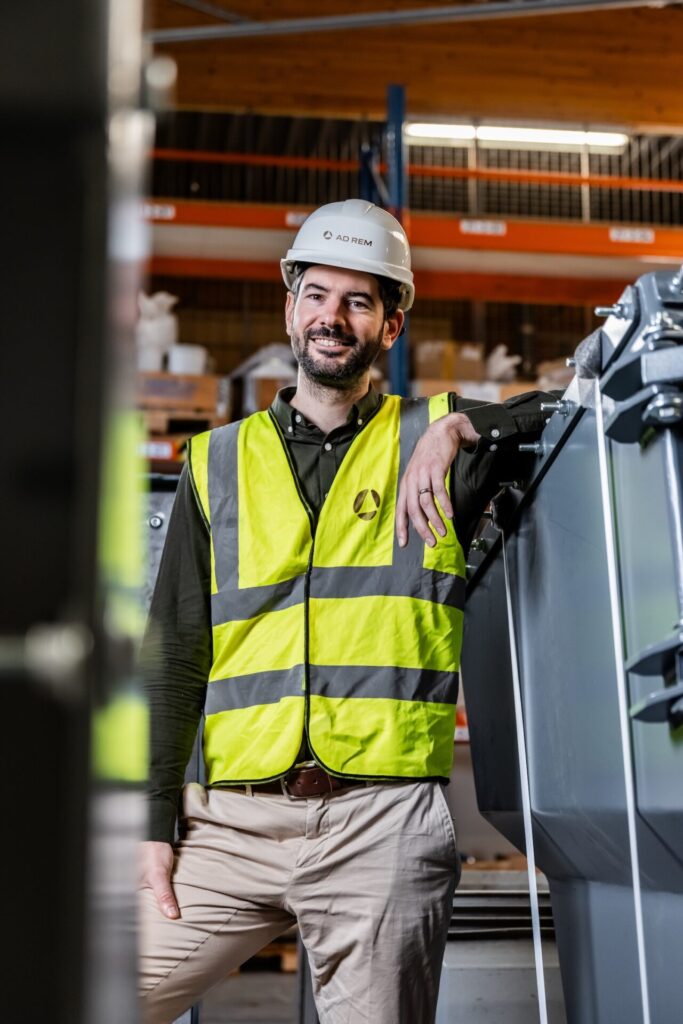
“The construction of our new building in Menen presented a great opportunity for us to go forward with our testing facility”, Saint-Germain continues. “As we are expanding with Valtech, it made a lot of sense to include this project in the plans”. The designated space entails 140 m² for the wet part of the process, 100 m² for the dry part, and 45 m² of lab space. On top of that, about 1000 m² of construction, assembly and storage space will be added for Ad Rem.
Lay-out and test capabilities
Lots of thought has gone into the lay-out and capabilities of the new test and development center. On the one hand, it has to be state-of-the-art, and capable of processing customer samples. On the other hand, it is important to remain flexible, and make it easy to adapt the different parts of the process for research and optimisations.
“With the current lay-out, a good compromise has been reached”, says Saint-Germain. “The test and development center will contain most of the process steps used also in a large plant, but built in a modular way so different steps can be removed, skipped, modified or exchanged.“
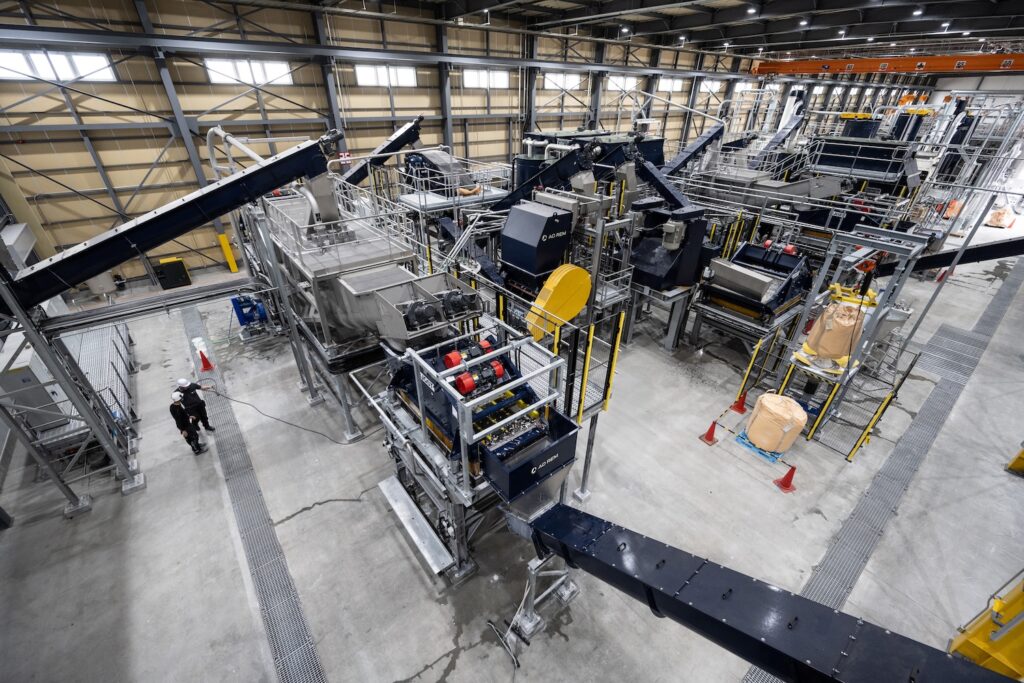
The process starts with a mobile feeding system for any rigid plastic mix. An air separation step is included to extract the light materials like foam rubbers and textiles. These are materials that can be used as RDF and should not enter the wet separation, since they soak up the separation medium and may cause issues. Then, a sieving step is provided with interchangeable screens to sieve off at different sizes. Typically, fines smaller than 4mm are sieved off. The test and development center will also house an offline shredder, to resize the material if necessary.
In the wet separation step, a downsized sink-float separator is used to separate the plastics at different densities. The original geometry was kept as closely as possible, since industrial circumstances have to be simulated. The separator has some modifications so the location of infeed can be changed, and process parameters can be adapted. Once fully operational, throughputs of 1 tonne per hour will be attainable – while current separators go up to 8 tonnes per hour.
Finally, the line will include a dryer for the outputs and big bag systems for storage.
“We are also looking to expand in what we are able to do regarding analysis and quality control, both in-line and offline. How that will be filled in exactly remains to be seen”, Saint-Germain adds. One thing he can share is the sampling device they are working on. “We combined different spectroscopic technologies to determine the plastic type, as well as the embedded molecules, and we have automated this otherwise time-consuming process. This will enable plastic recyclers to take a sample of flakes and scan it automatically, telling them within the hour not only how pure their output is, but also how much bromine or chlorine is present. So far, this is contained within a research project, but it is now running at its end and we expect our device to be commercially available by 2026”.
CFD analysis and optimisation
Aside from processing customer samples and trying out new methods, the test and development center will also be used to optimize existing processes. For example, Ad Rem partnered with Belgium-based AM Team to perform CFD or Computational Fluid Dynamics analysis on the sink-float separator. This enables a thorough analysis of the process flows inside the separator, and allows for the creation of a model, which can be used to simulate changes in the process parameters and design of the system. A similar approach was already successfully implemented for the Ad Rem heavy media plants, specifically for the metal separation drums, where misplacement of materials was reduced to near-zero.
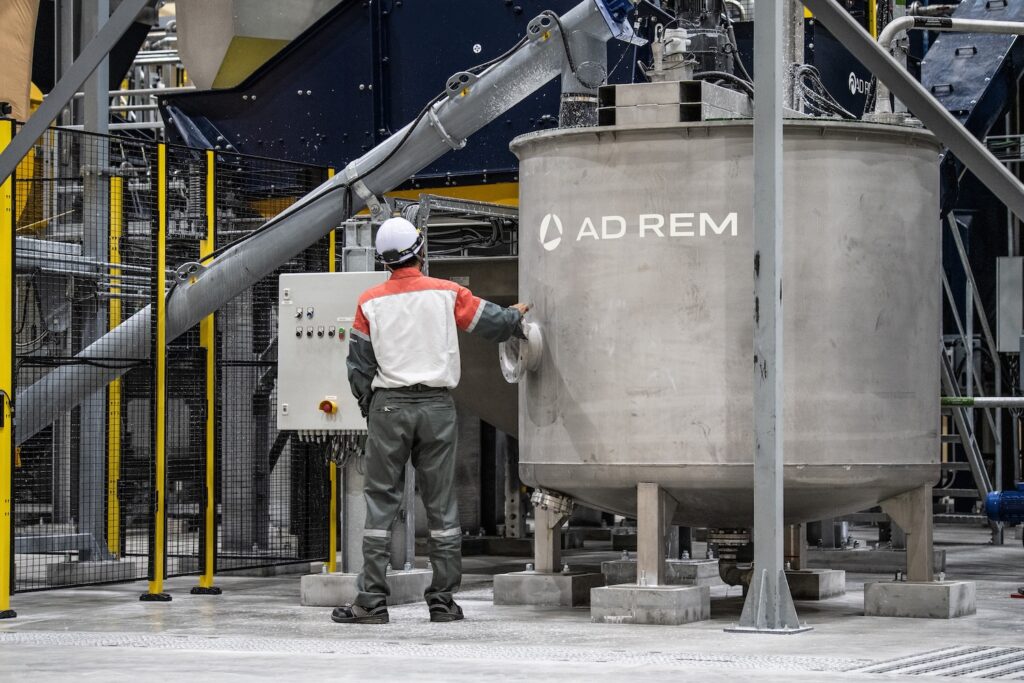
Through further optimisation of the different process steps, Ad Rem hopes to increase the return for their customers. “The final quality of the outputs determines their value. Process stability, medium density consistency, automation, and full control over the process is what makes the difference between selling your plastics back into the automotive industry for a good mark-up, or ending up making plastic bricks or garden furniture. The latter is much harder to remain profitable”, Saint-Germain concludes. “It’s also less circular”.
The new test and development facility will be built just down the road from the current Ad Rem offices in Menen, Belgium. The first visits and customer trials are expected to take place in the beginning of 2026.