As opposed to the more traditional flotation systems, the new Konstantinidis Bros SA plant will be a high-tech, state-of-the-art installation doing much more than just separating materials. Upon completion, it will deal with over ten tonnes per hour of mixed plastics and metals.
Scavenger as pre-treatment
Konstantinidis Bros SA was established in 1971 and is Greece’s largest recycling company. The new HMS plant is not the first project Ad Rem is doing for them. In 2018, a so-called “Scavenger” system was commissioned at their main production facility in Thessaloniki. The Scavenger is a compact machine, combining several sieving and wind sifting steps. This way, a fines fraction is created, as well as a light fraction which is suitable for waste-to-energy applications. The remaining fraction is called “SHF” or Shredder Heavy Fraction and contains all the plastics and metals. Free from fines and light materials, this fraction is ideal to be entered into the HMS system.
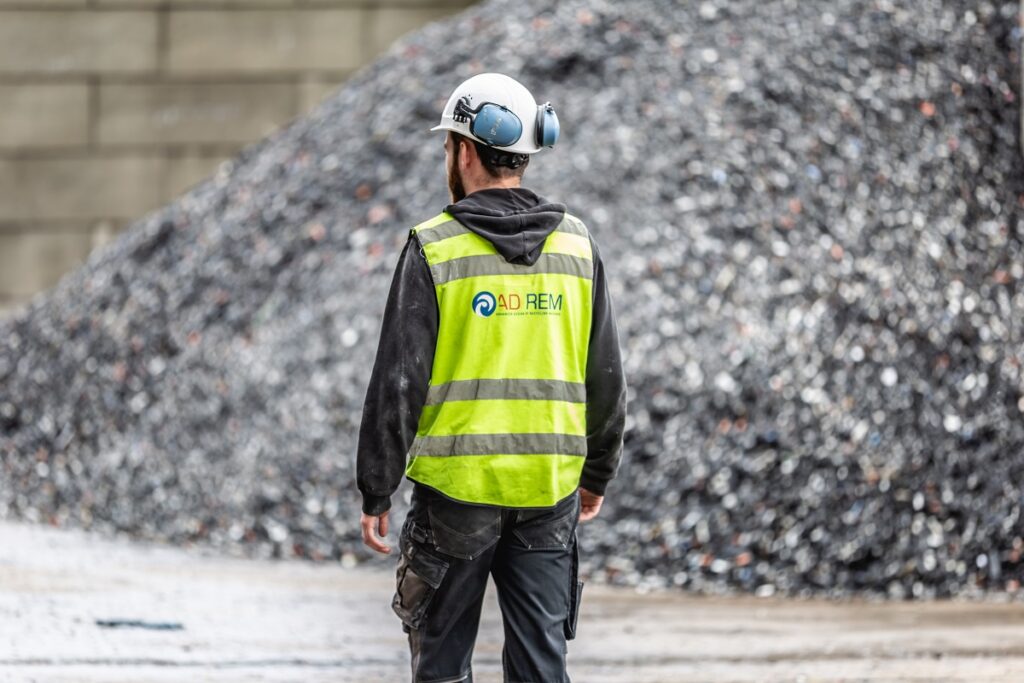
Patented innovations
The new HMS system will be the result of many years of innovations. Galloo, Ad Rem’s parent company, started developing flotation plants for metal recovery already over thirty years ago. But even though the core technology has a long and proven track record, new developments have never ceased.
Glancing at the new plant in Greece, one can immediately see an elaborate washing system. With rules and regulations becoming ever so strict, having a good water treatment has become increasingly important. Aside from complying with local regulations, the additional benefits of a proper washing system are that the medium stays clean, the separation process remains stable, and pollutants are concentrated in a single sludge output. To arrive at a well-functioning water treatment plant, Ad Rem can rely on the expertise of both Galloo and sister company Trevi Environmental Solutions.
Going a bit further down the material flow, other innovations become apparent. Instead of vibratory rinsing screens, rinsing drums are added at both output sides of the separation drum. This enables cleaning of the sieves while in operation. Not only does this prevent frequent maintenance stops, it also prevents medium losses. By using this innovation, the plant will consume the lowest possible amount of medium, while remaining operational on a 24/7 basis, except one shift per week for cleaning and general maintenance.
A double medium storage system can be seen as well. With this system, the operator will be able to switch the density of the system in a very short amount of time. This way, plastics can be separated from metals on a lower density, while magnesium or aluminium can be floated from heavy metals on higher densities using the same system.
University cooperation
Not all innovations are visible. The separation drum itself is the result of a study done together with the university of KU Leuven in Belgium. In this study, a computer model of the separation process was created and, using complex mathematics, the process and drum geometry were simulated for varying circumstances. The results of this study were implemented in the physical design of the plant with great success: when floating aluminium from heavy metals, the misplacement observed in both outputs approaches zero.
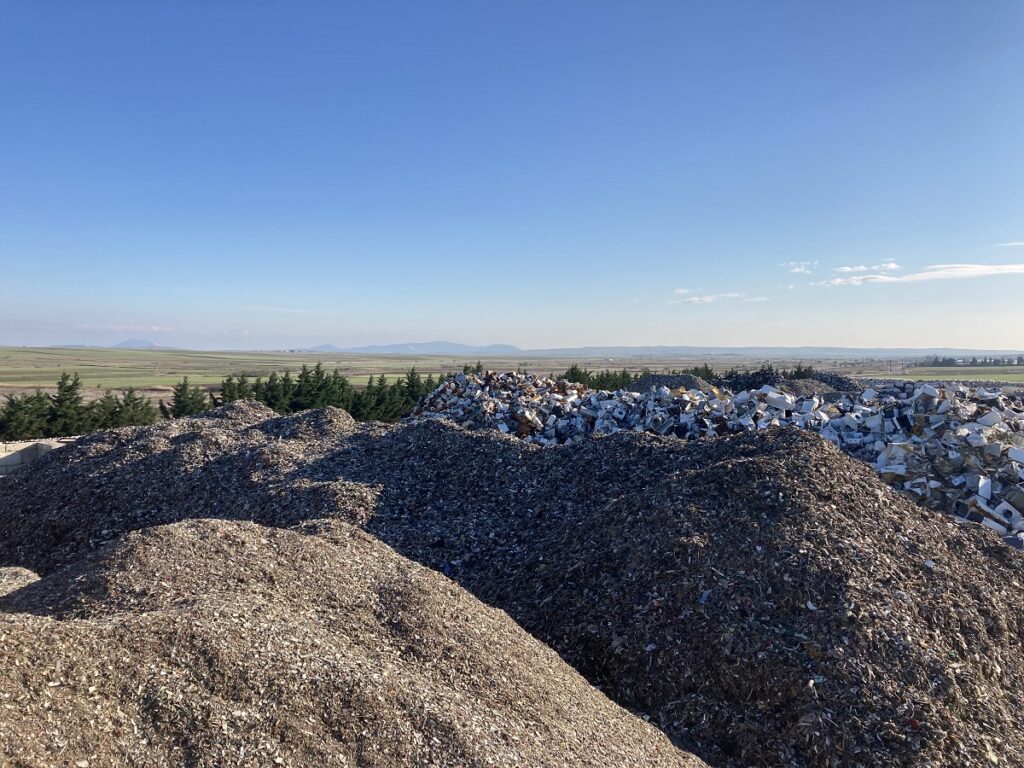
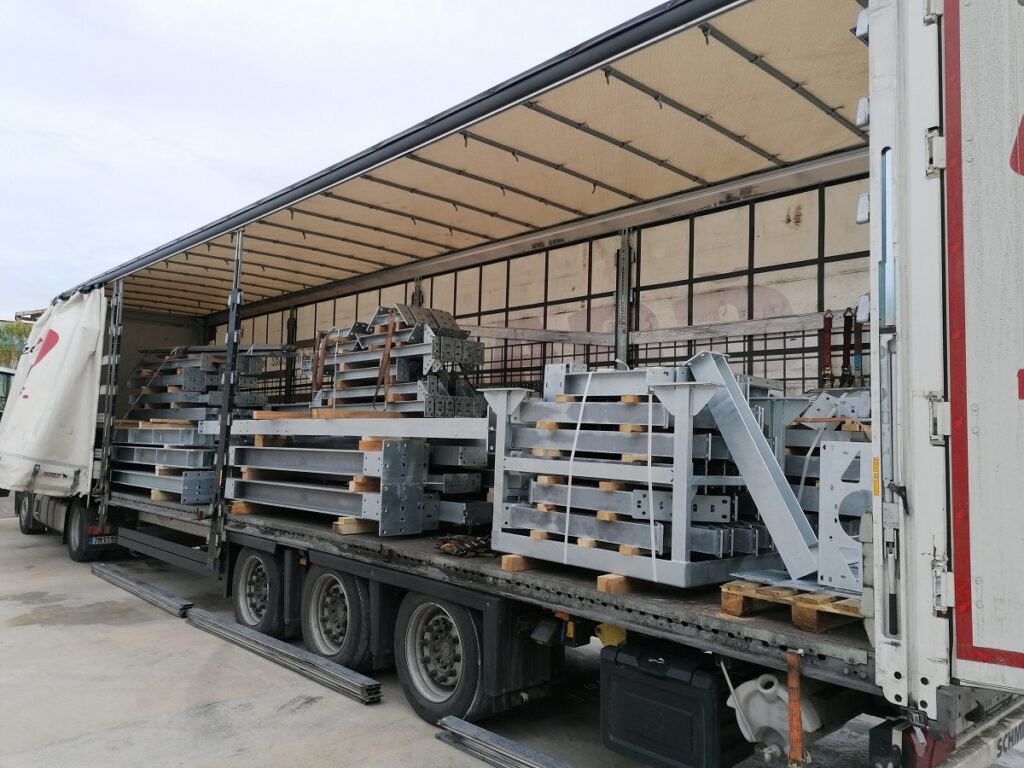
Process stability
A stable process leads to better results. That’s why a patented system was added to extract water from the medium, ensuring perfect control over the medium density and avoiding the need to add fresh medium every time the density needs to be increased.
But in the end, mechanical innovations can only do so much to increase the stability of the process. That’s why Ad Rem is focusing heavily on automation. All the innovations described earlier work without any operator interference. Frequency drives for most motors and pumps, sensors measuring the tank levels, automatic density measurement,… all ensure that the plant can operate most efficiently. Pump clogging up? The increased current will be visible for the operators so they can unclog it before the system stops. Density dropping? The automatic medium dewatering system will keep it up and stable. And so on..
Last, but not least, an interactive visualization and analytics system will store all plant data for years, and display it nicely in custom made graphs.
Conclusion
Back to Greece. Seeing the partly built-up plant is impressive, yet it’s hard to imagine the efforts that have gone into optimizing the underlying process. Ad Rem’s mission is to lead through technical innovation, and the new Konstantinidis Bros SA plant will be the best exemplification of that. Upon completion in early 2022, it truly will be the next generation flotation system.