A recent driver toward this has been the increased use of the output from anaerobic digesters (digestate) as a fertiliser which is applied to land. It is not seen as acceptable any longer to consign the non-organic rejects from food waste debagging and separation to landfill or incineration as a waste. It is not sustainable to use landfill, and even if it were, the costs are prohibitive and will continue to rise further as landfills are phased out across the EU, and elsewhere.
The renewable fertiliser from anaerobic digestion is now in heavy demand due to huge price hikes in mineral fertiliser costs since the pandemic. But, applying the output from traditional, size-reduced depackaging and separation equipment, raises a major concern about spreading small plastic (microplastic) particles on land.
It is now known that microplastic particles have entered every food chain on earth and are accumulating in our oceans. Now that cannot be good. At the very least, the industry should now adopt the precautionary principle. That being to avoid discharging any more microplastics while the scientific community studies the effect of this alien presence on global ecological systems and on our own bodies.
That’s the problem. Here is the solution:
Avoiding Microplastic in Food Waste
Flexible plastics of all kinds are invariably present in large quantities in food wastes and while size reduction is undoubtedly invaluable for its ability to chop up long fibres and reduce plastic packaging including plastic films to small chips which might otherwise block and clog systems, other techniques have been found. The new equipment uses innovative physical methods to avoid the tiny plastic pieces called “microplastic” and wins still further by providing:
- much better purity of the “light rejects” stream (usually mostly comprising flexible plastics) and hence he opportunity for the opened film bags (pulled out whole), plastic bottles, ready-meal packets etc., to be placed on a general MRF or ERF recycling conveyor line for further polymer specific sorting by, for example ballistic separation
- the opportunity for the non-recyclable plastics to at least hold a sufficient calorific value to be sold for incineration as SRF or RDF
- metal items are ejected whole or if not, in no more than 3 pieces, enabling efficient metals recycling rather than the loss of valuable metals and polluting heavy metal content within the rejected heavy fraction.
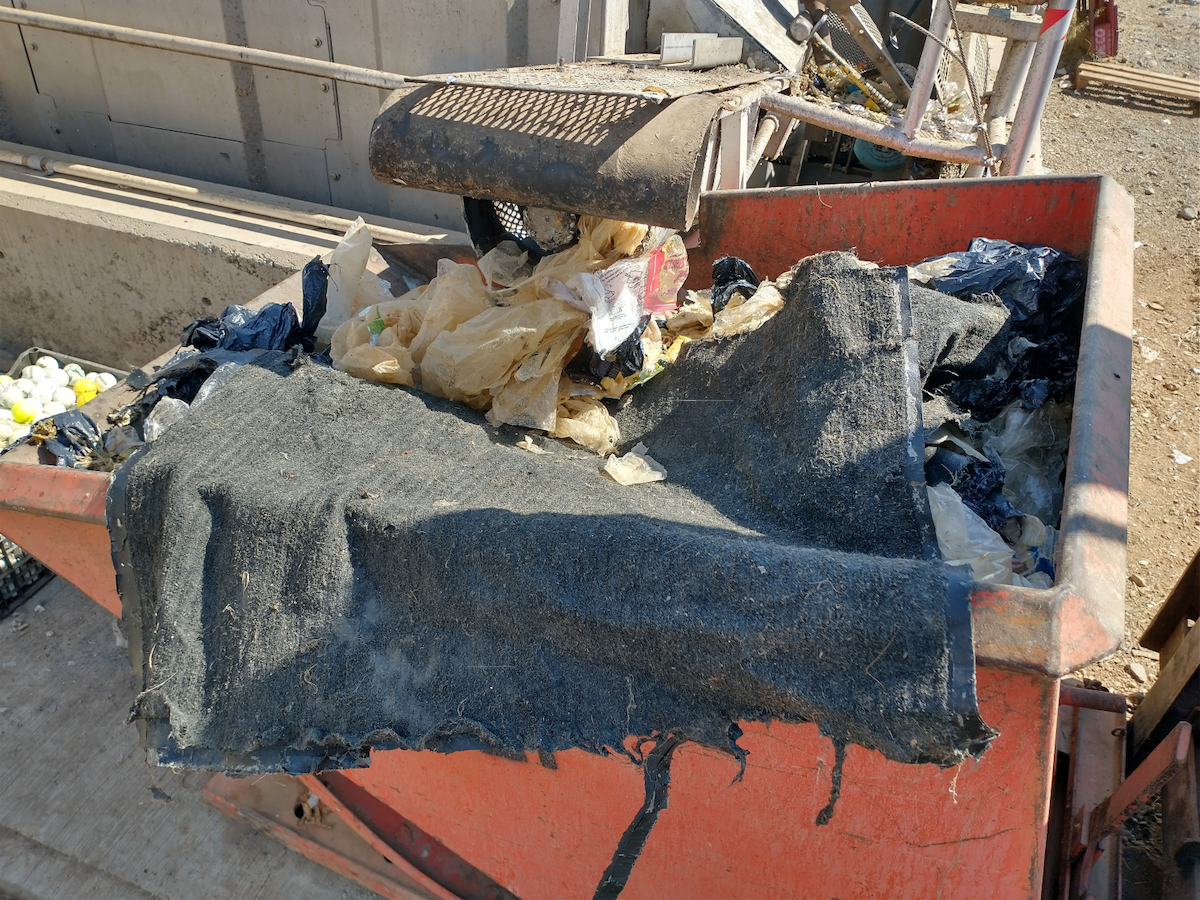
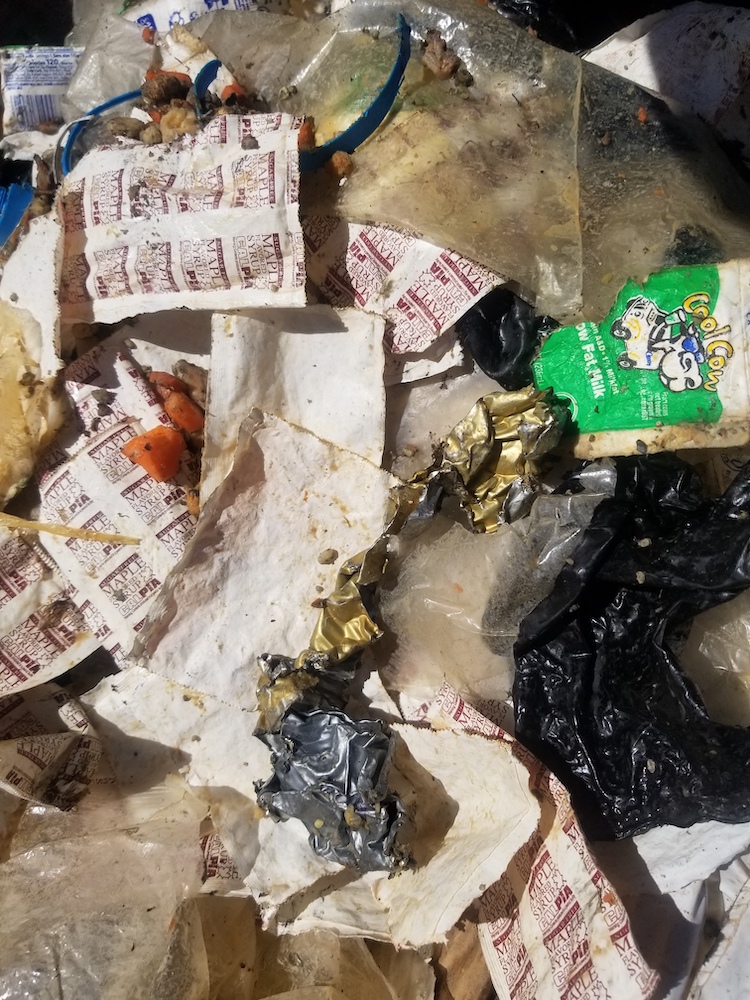
New Depackaging Systems Use Less Power
There are energy efficiency gains alongside avoidance of microplastics in the reject streams. Size reduction is very energy intense and with rising energy costs the lower consumption of less destructive Depackaging and separation is a big asset.
How the Twister™ Depackager and Separator Works
An example of this new technology is the purpose designed Twister™ by Canadian company Drycake™.
The new Twister 3rd generation range has been in development since 2016. It is suitable for centralized organic processing with unmatched separation performance has just been introduced globally after an initial distribution in Canada and the US during 2021.
At the feed hopper contrary rotating twin augers provide blockage and hang-up prevention for reliable debagging. Optional digestate or process water is added.
The feed (wetted or dry) enters the main processing stage horizontally and starting low in the unit is subjected to a high-speed air vortex (if wet an air-entrained water vortex) induced by the angled stub-arms on the rotating shaft. Turbulence pushes the water and organic material (or organic powder and crumbs if dry) out horizontally where it drops through a perimeter filter.
Meanwhile, the angled stub-arms (or plates) knock heavy solid items upward out of the lower submerged zone. On the same route the light items are sucked, plucked and blown upward until they are also ejected at the top by centrifugal forces. Cleaning and drying takes place in the high velocity airflow where the heavy items and the plastic are bashed vibrated and flexed, shaking off anything still adhering to the surfaces.
The goal is to completely expel each packet opened, emptied, clean and whole, or in a just a few pieces. The “twister” effect produces clean organic pulp (or dry) output that is free of microplastics, so anaerobic digestion can begin right away.
The light fraction is baled and sent to specialist plastics reprocessing, despatched, as SRF/ RDF, or may introduced to source segregated household or commercial waste flows for further sorting, metals removal and ballistic separation for extracting the valuable plastic polymer items such as PET bottles etc.
Plastic bags and films are prevented from becoming wound around the shaft using a patented method. The system avoids clogging and blockage. Tests show 99.8% organics removed. Up to 20% solids in the pulp, and has an industry leading uptime.
The short ROI on this equipment when waste disposal costs are converted to saleable commodities means that customers are decommissioning existing equipment early where there is a strong business case to upgrade.
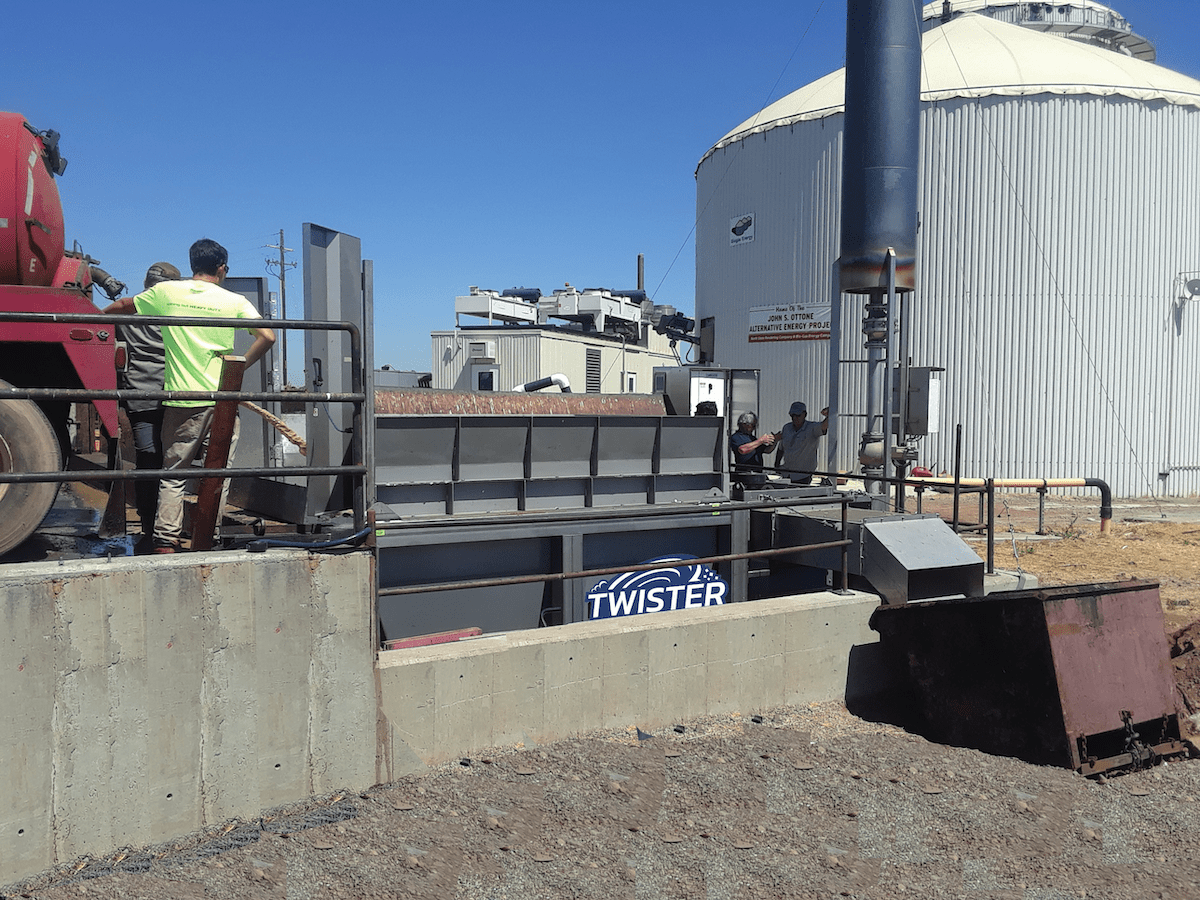
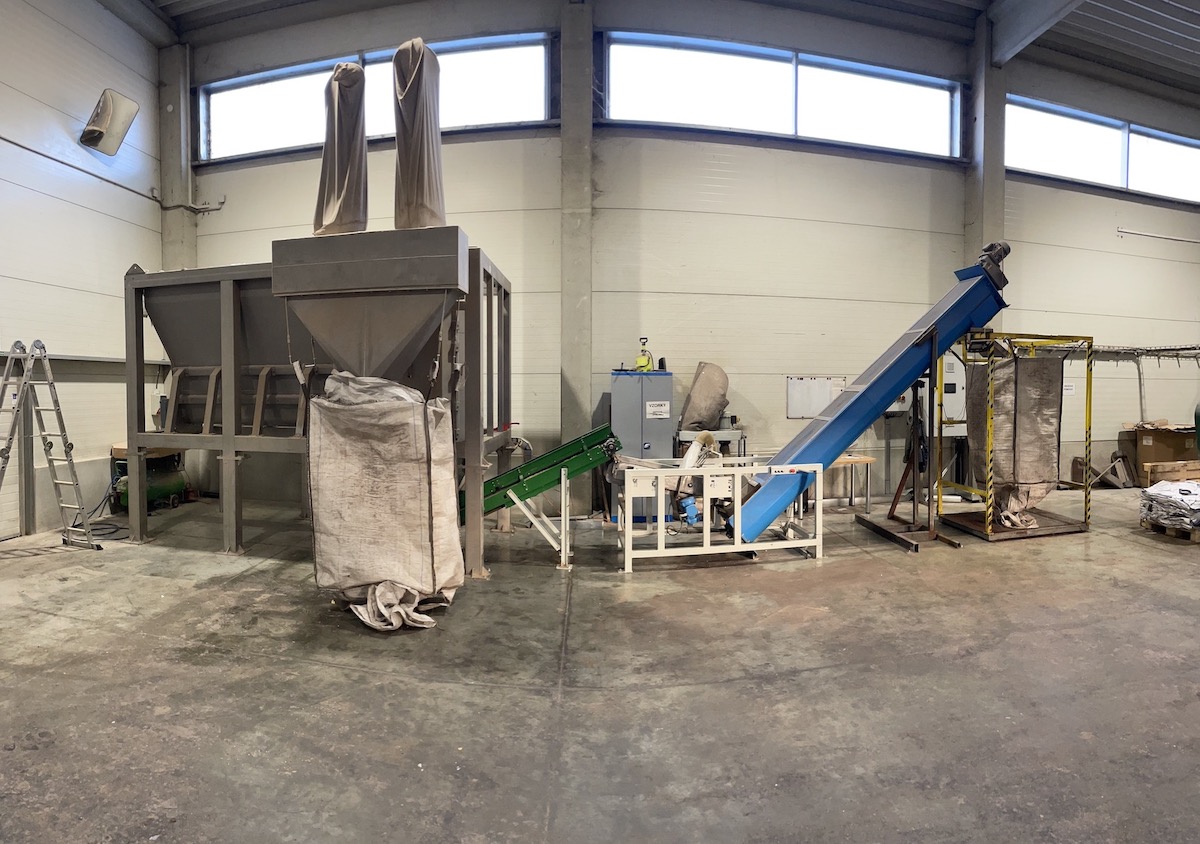