Now a new version of the ReTec mineral wool recycler has been sold to a customer in Scandinavia. As the name of the machine says, the machine can process mineral wool for recycling.
From landfill…
Used insulation material of either stone wool or glass wool has previously ended up in landfills and especially in Denmark, the eyes have been opened to the see the possibility of recycling the material. ReTec sold the first mineral wool machine to a customer in Denmark back in 2012 and since several customers have opened their eyes to what the machine can accomplish, therefore ReTec recently launched an improved version of the machine.
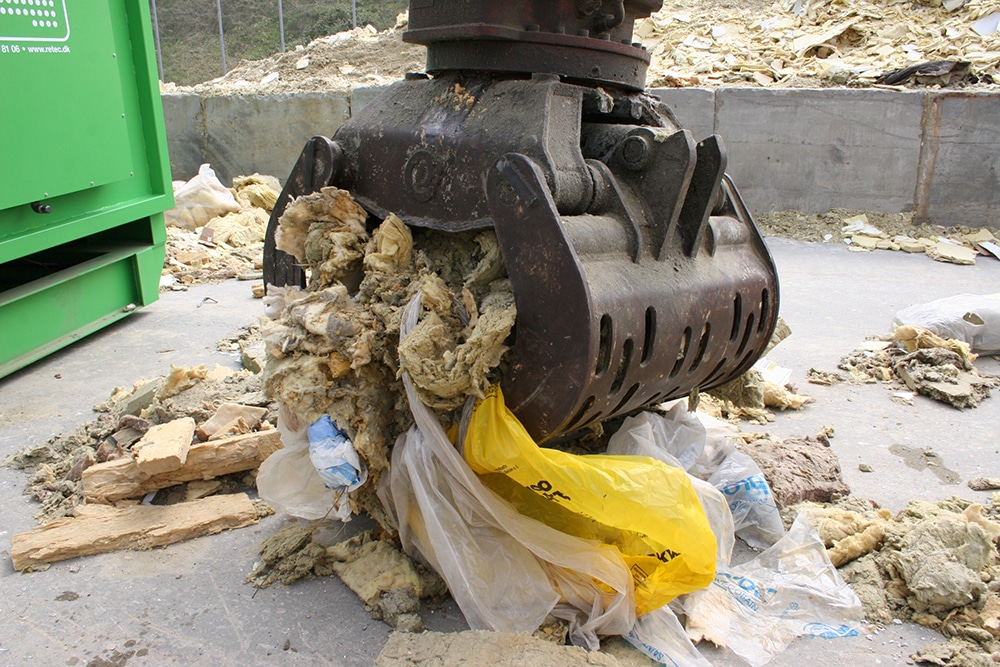
Simple process
The process is relatively simple. The material is fed into the hopper of the machine. From demolition companies, recycling sites, and new construction, the insulation material may contain impurities such as nails, screws, rubble, wood, and other material. Everything is pressed through the first part of the machine and in the second part, the mineral wool is sorted out. The volume of the mineral wool is reduced up to 20 times the volume and through the sieve, the reject is sieved. The final product can be recycled to produce new mineral wool or for other purposes. The capacity of the process is at least 5 tons per hour, depending on the desired final product.
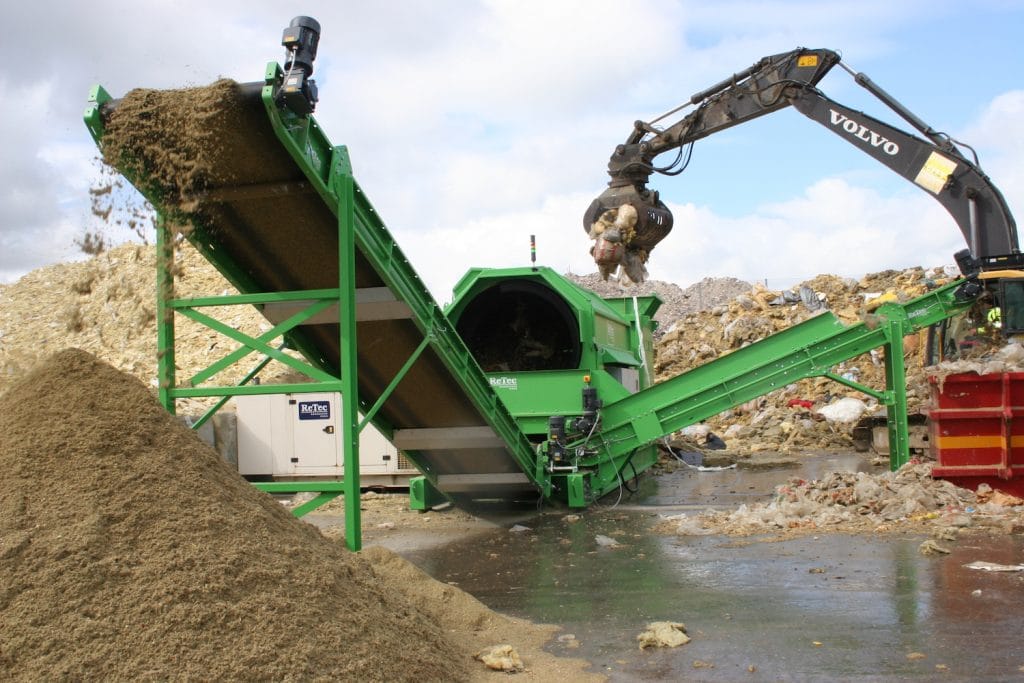
… to recycling and green solutions
Jan Frydkjær Pedersen, sales consultant export, who has sold this plant to the customer in Scandinavia, has closely followed the various stages in the process of the new version of the mineral wool recycler. ”My client has a business idea where it is possible to recycle mineral wool for a variety of purposes. I think it is great that more countries and companies are getting interested in having to recycle materials that used to be landfilled. The major advantage of the mineral wool recycler is that in one workflow it can produce a recyclable final product. I know that other potential customers are trying solutions that may require more machines and thus more energy to achieve the same result. I hope that more people will realize the opportunities that ReTec can offer, Jan says and continues: ”Mineral wool tends to cause severe wear. Of course, this has been taken into account, so the replacement of wear parts is limited and quick. The machine is extremely efficient and has a wealth of setting options so that customers can have it set up to meet their desired end product. I am happy to be a part of these green solutions that can benefit both the environment and our society,” concludes Jan Frydkjær Pedersen.
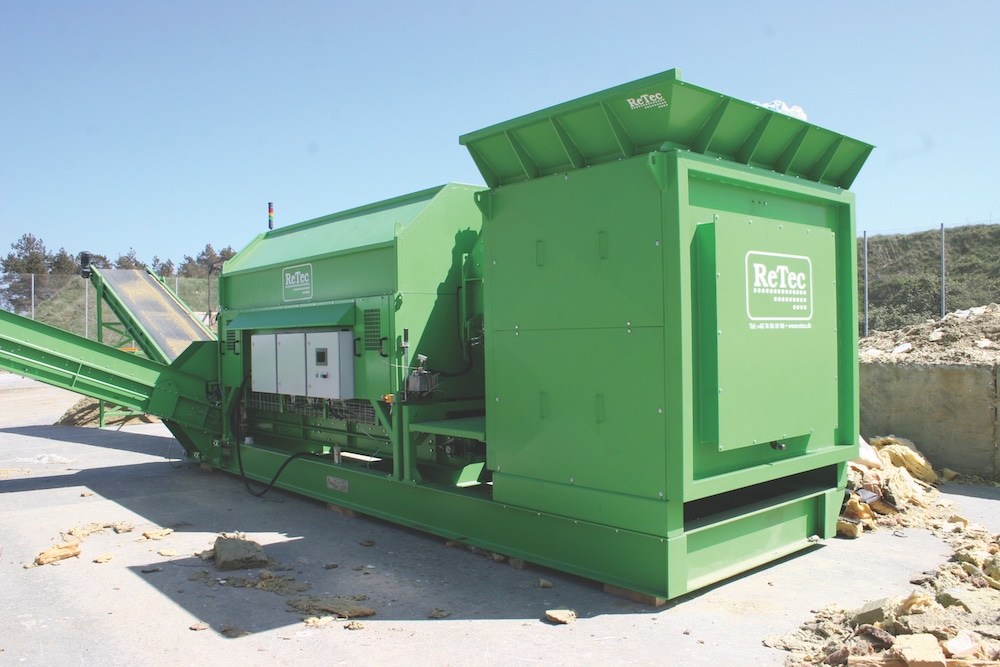